Keep up to date with us on the latest industry news as well as what's going on at True Gear & Spline Ltd. We also post articles for insider tips and tricks, so make sure to check back frequently.
Discussing The Art of Gear Cutting
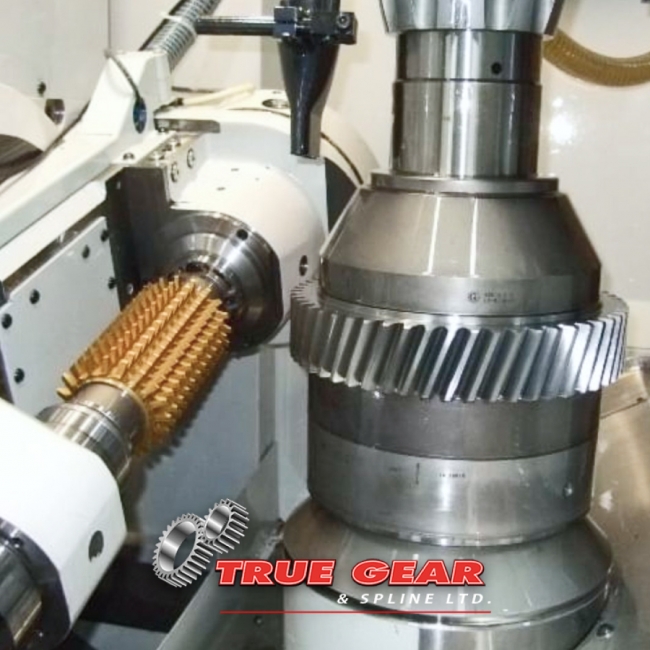
Gear manufacturers are trusted with manufacturing custom gears to meet the specific requirements of their clients. They rely on cutting-edge technology and sophisticated gear-cutting techniques to manufacture custom gears accurately. The margin for error is very low in gear manufacturing as even the slightest mistake can have detrimental effects. If not manufactured precisely, faulty gears can bring the entire operations of industries and businesses to a halt. This blog explores the world of gear cutting and briefly discusses all you need to know about gear cutting. Read this blog until the end to make an informed decision.
The History of Gear Cutting and Its Evolution
It might sound unbelievable but humans have been leveraging the power of gears for thousands of years. Of course, our ancestors relied on more primitive gears owing to the limitations of technology back in those days. The initial phase of commercial gear manufacturing that we know today can be tracked to the 19th Century. It wouldn't be false to say that the Industrial Revolution spurred the gear manufacturing industry and gave birth to many mass production techniques like hobbing and shaping.
Fast forward to current times, gear manufacturers leverage the power of technologies like computer-aided design (CAD) and computer numerical control (CNC) machines to offer flawless gear-cutting services. The evolution of the gear cutting techniques reflects the progress that we humans have made.
It is almost impossible to imagine the world without gears. They are a vital component in industrial equipment, appliances, and vehicles.
The Process of Gear Cutting: From Design to Production
Gear cutting is an intricate process that involves many nuances and intricacies. Only expert gear manufacturers must be trusted with such difficult tasks. The process of converting raw materials to gear blanks and then to custom gears is captivating. Choosing the ideal metal for manufacturing gear blanks is the first step in the gear-cutting process. Steel, cast iron, bronze, and aluminum are all suitable for manufacturing gears. However, steel and cast iron stand out owing to their strength and load-bearing abilities.
The next step is to manufacture gear blanks in the dimensions requested by the customers. Choosing the suitable gear-cutting method is also a crucial step in the gear manufacturing process. Hobbing, milling, grinding, and broaching are all popular gear-cutting types. The gear manufacturer chooses the apt gear-cutting method depending on factors like the size, volume, and turnaround time of the order.
Finishing processes like heat treatment or surface coating may be applied to enhance durability and performance. Rigorous testing is done to ensure that each gear meets quality standards before being ready for use in various applications.
Advantages of Gear Cutting Techniques
1)Precision
The scope for error is minimal in gear manufacturing and modern gear cutting techniques guarantee precision. Modern gear-cutting tools can manufacture gear with precision, thus ensuring smooth operation and seamless torque transmission.
2) Customization
The dimensions in which gears need to be manufactured depend on client requirements. The flexibility gear cutting offers empowers gear cutters to offer custom gear manufacturing. This means gears can be tailored to specific requirements, such as size, shape, and material composition.
3) Efficiency
This is one of the most crucial advantages of gear cutting as far as gear manufacturers are concerned. Modern CNC gear cutting ensures minimal wastage of materials and guarantees quick turnaround time. While the initial investment of gear-cutting machinery might be expensive, it offers a cost-effective solution to gear manufacturers in the long run.
Gear Cutting From True Gear & Spline Ltd.
We offer 5-axis CNC gear-cutting services at the best rates to clients in Toronto, GTA, and Ontario. We have invested in state-of-the-art gear cutters, allowing us to offer flawless gear-cutting services with quick turnaround times.
Our gear-cutting methods allow us to cut gears up to 3 meters in diameter. What's more? We can manufacture spline shafts, timing pulleys, sprockets, and gear racks, apart from different gears. You can rely on us for steel, aluminum, bronze, phenolic, and nylon gears.
Customization is at the heart of everything we do at True Gear & Spline Ltd. Through our continued efforts, we have earned a reputation as the best gear manufacturer in Ontario. We boast 28 gear hobbers, Gleason Pheonix 400GH, and Mitsubishi GE20A. Get in touch with us for all your custom gear-cutting needs.
Conclusion
True Gear & Spline Ltd. in Cambridge, ON, is a one-stop destination for all your gear-cutting needs. We manufacture spur, helical, bevel, and worm gears. We can also manufacture custom splined shafts as per your requirements. Call +1 519-653-1301 to place an order or avail of our gear-cutting services.