Keep up to date with us on the latest industry news as well as what's going on at True Gear & Spline Ltd. We also post articles for insider tips and tricks, so make sure to check back frequently.
Enhancing Gear Production Efficiency Through Gear Hobbing
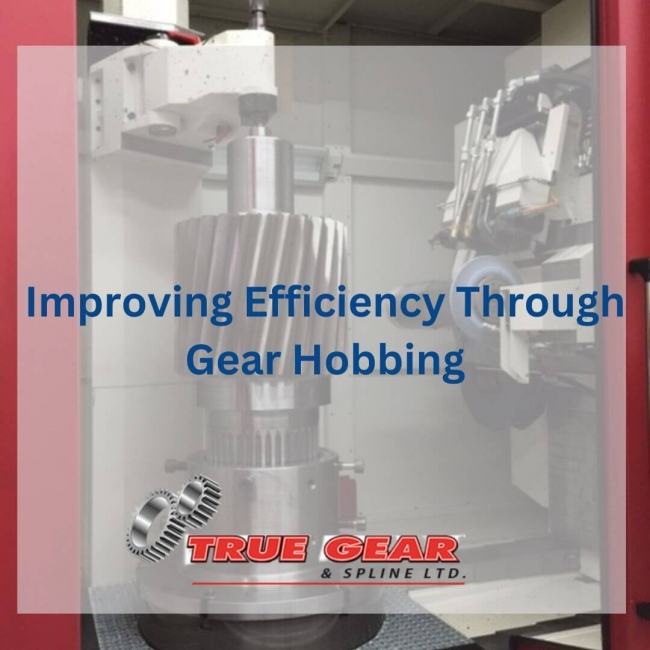
Gears are the unsung heroes of countless industries. Very few people are aware that gears are responsible for keeping the industrial world up and running at all times. There are hardly any industries that do not rely on gears or splines to facilitate effective torque transmission. and keep production cycles running From automobiles to heavy machinery, gears play a critical role in transferring power and ensuring seamless operation. Have you ever wondered how these intricate mechanical components are produced with such precision? Enter gear hobbing – the catalyst facilitating flawless gear manufacturing. In this blog post, we discuss how gear hobbing helps gear manufacturers achieve efficiency and accuracy every time.
Understanding Gear Hobbing
Hobbing is a significant process that plays a vital role in manufacturing gears with precise tolerances. We elaborate further to help you understand what exactly is gear hobbing. Hobbing is a simple method used for cutting teeth into gear blanks.
There is no dearth of sophisticated hobbing machines in the market today. Different types of hobbing machines are suitable for specific applications. There are different types of gear hobbing machines available today, each designed for specific applications. CNC (Computer Numerical Control)gear hobbing machines are among the most popular owing to the ease of operation and quick turnaround time they offer. These machines are controlled with the help of software. The operator simply instructs the CNC hobbing machines with the help of a computer and software and the machine does exactly as instructed.
Key Benefits of Gear Hobbing
Enhanced efficiency
The ability to enhance efficiency in the gear production process is what makes gear hobbing popular among gear manufacturers. While gear shaping and milling are also viable options, the ability of sophisticated hobbing machines to reduce production time is unmatched. Gear hobbing allows for the simultaneous cutting of multiple teeth, resulting in faster and more efficient manufacturing processes.
Precision
There is hardly any margin for error in gear manufacturing. By using sophisticated and specialized gear hobbing machines, manufacturers are able to produce high-quality gears quickly without sacrificing precision and accuracy. The rotating gear hobbing cutter cuts into the workpiece quickly and with ease to create all types of tooth profiles, thus helping gear manufacturers be versatile. The use of CNC technology further enhances precision by ensuring consistent and repeatable results.
Cost-effectiveness
Paying attention to and making use of cost-effective methods is crucial for gear manufacturers in order to maximize their profits. In mass production scenarios, gear hobbing proves to be very cost-effective. The ability of hobbing machines to cut multiple teeth at once and reduce cycle times makes them very reliable and cost-effective. Since gear hobbing produces accurate and reliable gears, there are fewer instances of rework or scrap material, further contributing to cost savings.
Gear Hobbing Process
Gear hobbing is an intricate process that involves work at multiple levels. We take a closer look at the hobbing process and hope to simplify it for you.
Preparing the workpiece and setting it up properly in the hobbing machine are important steps in the hobbing process. Any mistake in this step can make it difficult for gear manufacturers to achieve accurate gear production. The workpiece is generally made from steel or other hard metals. This is because the gears need to be durable and be able to facilitate torque transmission without breaking. The workpiece is properly positioned on the hobbing machine to ensure flawless cutting.
Tool selection and assembly come next in the hobbing process. Selecting the right cutting tool depends on a wide range of factors like tooth profile requirements and the choice of material. The selected cutter is then assembled onto the machine spindle with precision.
Any gear manufacturer with experience and skills knows the importance of feeding mechanisms. A combination of rotation and linear motion drives the cutter. Hobbing machines do so while carefully synchronizing the workpiece with the rotation of the cutter. This ensures that each tooth is accurately cut. Chip removal plays an important role in maintaining efficiency during this process. Gear manufacturers put special mechanisms in place to remove chips generated during cutting without interrupting the machining operation.
Cooling and lubrication are sacrosanct to ensure a smooth gear hobbing process. Without appropriate lubrication, there is a risk of damage to both the workpiece and the hob. Coolants are used to control temperatures generated due to the friction between the tool and the workpiece.
Real-World Applications
Automobile industry
Transmission gears widely used in the automotive industry are manufactured with the help of hobbing machines. It is important for transmission gears to be smooth. Drivers might end up experiencing untoward incidents on the road if the transmission gear of their vehicle is not smooth. The precision and efficiency offered by gear hobbing machines ensure smooth shifting of gears, resulting in improved vehicle performance. Gear manufacturers are able to deliver top-of-the-lines required for sophisticated transmission systems that are a crucial part of modern automobiles.
Heavy machinery industry
Heavy machinery is widely used across many industries like mining, construction, and shipbuilding. These machinery rely on a lot of moving parts to ensure optimal performance. Gear hobbing finds application in producing large-scale industrial gears used in construction equipment, mining machinery, and power transmission systems. These massive gears require high accuracy and strength to withstand heavy loads and extreme conditions. Gear hobbing machines enable manufacturers to achieve precise tooth profiles that ensure optimal power transmission and durability.
Conclusion
As we have seen in this blog, gear hobbing is a crucial process that helps gear manufacturers enhance efficiency and achieve precision in gear production. The ability of sophisticated hobbing machines to cut multiple teeth simultaneously reduces production time, enabling gear manufacturers to maximize profit and reduce turnaround time. The CNC gear hobbing machines help gear manufacturers to flawlessly achieve precision. We at True Gear & Spline Ltd. harness the power of gear-hobbing machines and leverage advanced technologies like CNC, enabling us to stay ahead of the competition. Our expansive facility is equipped with all the latest tools and equipment required to manufacture all types of gear with a quick turnaround time. We manufacture spur gears, and helical gears, and offer services like gear shaping and CNC machining at the best rates. Get in touch with us today to learn about everything we can do for you.