Keep up to date with us on the latest industry news as well as what's going on at True Gear & Spline Ltd. We also post articles for insider tips and tricks, so make sure to check back frequently.
Explaining Gear Shaping & Gear Hobbing
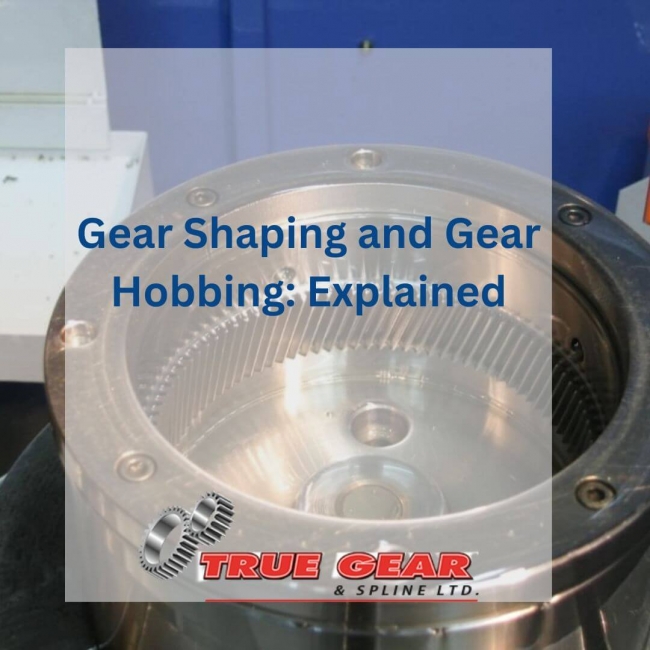
Introduction to Gear Shaping
The small interlocking teeth are a distinctive feature that we all associate gears with. These teeth are crucial to a gear's functioning and help machines run smoothly. But have you ever wondered how those tiny teeth are cut and shaped? That's where gear shaping and gear hobbing come in. These two processes are essential for gear teeth cutting and shapingt. Teeth cutting and shaping are crucial for manufacturing high-quality gears used in everything from cars to industrial machinery. In this blog post, we'll learn about gear manufacturing and explore what gear shaping and gear hobbing entail, their advantages, when they're used, as well as significant differences between them.
Advantages of Gear Shaping
The gear shaping process is considered highly effective because it produces teeth with a more precise shape and size. This results in gears that have lower noise levels during operation, longer life, and improved efficiency.
Versatility is another significant benefit of relying on a gear shaping machine. Versatility in the sense that this process can create a wide range of gears, including spur, helical, bevel, internal gears and more. What’s more? Modern gear-shaping machines have the strength to work on even the hardest material like steel alloys or non-ferrous metals.
Gear shaping process also allows for greater design flexibility than many other processes because it requires fewer tooling changes during production runs. This means that manufacturers can easily make modifications to their designs if necessary without having to stop production entirely.
When is Gear Shaping Used?
Gear shaping process is a highly specialized manufacturing technique that involves cutting teeth into a gear using a specially designed cutter. It is often preferred over other methods of gear production when the required accuracy and precision are high, and the volume of production is low to medium. In particular, it is an excellent choice for producing gears with complex shapes or non-standard tooth profiles. If the gears require tight tolerances that cannot be achieved through other means or have unique geometries that demand precise cutting techniques, then gear shaping may be the best option available. Additionally, because this process can create extremely strong and durable gears due to their uniformity in size and shape without any stress concentration points on them, it is frequently used in industries where reliability and longevity are crucial factors such as aerospace, defense or automotive engineering sectors where safety requirements are very strict.
Ultimately, choosing between different manufacturing processes depends on several factors, including cost-effectiveness, material properties involved in making gears as well as desired quality standards which should also be considered before making any decisions about how to produce specific types of gears optimally for each application's needs!
Introduction to Gear Hobbing
Gear hobbing process is commonly used to cut teeth into gears. It involves using a special machine called a gear hobber, which uses a rotating cutting tool to remove material from the workpiece and create the desired shape. The basic principle of gear hobbing is relatively simple: the cutting tool (known as the hob) rotates in sync with the workpiece, gradually removing material until the desired tooth profile is achieved. The speed and movement of both components are carefully controlled to ensure accuracy and consistency. If you're looking for an effective way to manufacture high-quality gears at scale, then gear hobbing could well be worth considering!
Advantages of Gear Hobbing
Cost-Effectiveness is one of the major advantages of gear hobbling process. It offers cost advantages, especially for large-scale production. Once the hob and machine setup is in place, the cost per gear decreases significantly. The efficiency of the process also contributes to lower production costs, making it an economical choice for gear manufacturing.
With gear hobbing process, you can also be sure of surface finish and gear quality. Gear hobbing produces gears with excellent surface finish and high-quality tooth profiles. The cutting action of the hob results in smooth gear surfaces, reducing friction and wear during gear operation. The precise tooth profiles ensure proper gear engagement and load distribution, enhancing the overall gear performance and durability.
When it comes to producing high-quality gears quickly and accurately at scale while retaining maximum material yield per workpiece; Hobbing remains one most preferred methods by mechanical engineers today
When is Gear Hobbing Used?
Gear hobbing is a machining process that is used to produce gears with precision and accuracy. It involves using a hob, which is a cutting tool made up of helical teeth, to machine the gear on a rotating workpiece. Gear hobbing process is typically used for creating spur and helical gears in large quantities or for complex designs that require tight tolerances. Additionally, gear hobbing can be utilized for producing splines or other types of intricate components that have similar tooth profiles as gears do. Gear hobbingspecifically refers to this highly specialized method of creating cylindrical shapes with teeth by removing material from the surface of the workpiece through cutting, making it ideal for creating custom-made parts where quality and consistency are critical factors. Overall, gear hobbing process remains an essential technique within manufacturing industries seeking efficiency when producing high-volume straight-toothed components while ensuring cost-effectiveness plus sustainability without compromising its performance capability over time.
Significant Differences Between Gear Shaping and Gear Hobbing
One significant difference between gear shaping and gear hobbing is their respective levels of precision. Gear shaping has a higher degree of accuracy due to its ability to make more intricate cuts, resulting in smoother and better-finished gears than those produced by gear hobbing.
Another key difference lies in their speed: gear hobbing can produce gears faster than gear shaping, as it's typically used for high-volume production runs. The choice between these two processes often boils down to the type of material being worked with and the requirement of the clients.
Both techniques have their strengths and weaknesses depending on specific requirements for each project. Understanding these differences will help manufacturers determine which process is best suited for their particular needs.
Conclusion
As discussed in this blog, it's important to note that both processes require expertise in handling complex machinery such as gear-shaping machines or hobbing machines. Therefore, it's crucial to choose a reputable manufacturer like True Gear & Spline Ltd. which has a proven track record in delivering quality products. We are one of the most popular custom gear manufacturers in Ontario with clients across Canada. Our state-of-the-art facility is equipped with the latest gear hobbing and gear shaping machines that allow us to meet all your gear and spline needs. Get in touch with our team today to discuss your gear manufacturing requirements.