Keep up to date with us on the latest industry news as well as what's going on at True Gear & Spline Ltd. We also post articles for insider tips and tricks, so make sure to check back frequently.
Gear Grinding Process: Technology, Benefits and Types
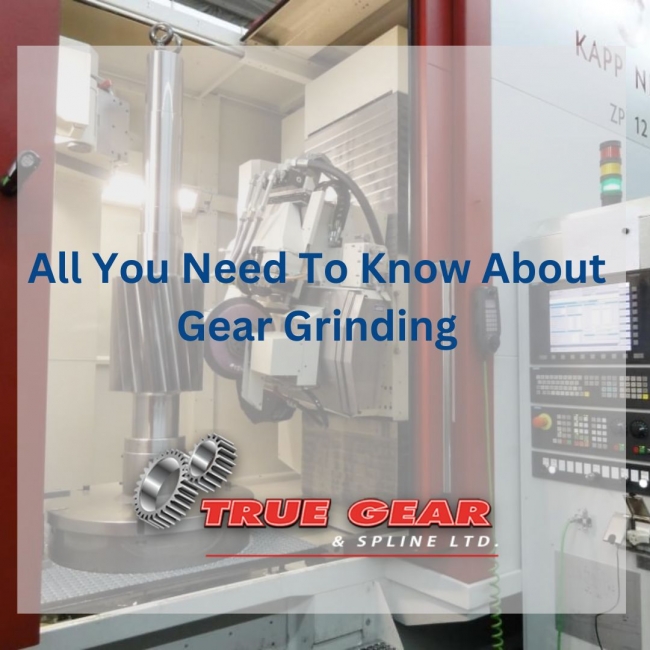
Ready to take your manufacturing process to the next level? Then it's time to delve into the world of gear grinding! This cutting-edge technology offers a multitude of benefits, from enhancing precision and efficiency to reducing costs and waste. But what exactly is gear grinding, and how does it work? In this blog post, we'll explore everything you need to know about this essential process - including its various types and applications.
What is Gear Grinding?
- Gear grinding is a process that uses abrasive machining to remove material from a workpiece in order to generate the desired shape. The most common type of gear grinding is called external gear grinding, which is when the teeth on the outside of the workpiece are ground down.
- External gear grinding can be done either by generating or form grinding. Generating grinders use a wheel that moves in a linear motion, while form grinders use a wheel that moves in a rotary motion. Both types of grinders can produce very accurate results, but form grinders are generally more expensive and have longer setup times.
- The main benefit of gear grinding is that it allows for very tight tolerances to be achieved. In many cases, gear grinding is the only way to get the level of precision required for certain applications. Additionally, gear grinding can extend the life of a workpiece by increasing its wear resistance.
- There are several different types of gear grinding, each with its own advantages and disadvantages. The most common types are profile grinding, continuous path grit belt grinding, and plunge cut face hobbing.
- Profile grinding is best suited for small batches of parts with simple shapes, while continuous path grit belt grinding is better suited for large batches of parts with more complex shapes. Plunge-cut face hobbing is typically used for high-precision workpieces where very tight tolerances need to be met.
Basic Methods for Gear Grinding
There are three main methods used in the gear-grinding process:
1) Stock removal: Stock removal is the most common method used in the gear grinding process. This method involves removing material from the workpiece to achieve the desired shape, size and surface finish. The material is removed using abrasive wheels or belts that rotate at high speeds. The amount of material removed depends on the type of abrasive wheel or belt used, the speed at which it rotates, the pressure applied to the workpiece, and the feed rate.
2) Form grinding: Form grinding is another common method used in the gear grinding process. This method uses a shaped abrasive wheel to remove material from the workpiece to create the desired shape. The advantages of form grinding over stock removal include increased accuracy and improved surface finish. However, form grinding can be more time-consuming than stock removal.
3) Shaving: Shaving is the third main method used in the gear grinding process. This method uses a rotating cutter to remove small amounts of material from the workpiece until it reaches the desired shape, size and surface finish. Shaving is typically used for finishing gears and can produce very accurate results. However, it can be a slow process compared to other methods.
Benefits of Gear Grinding
Gear grinding is a process that can be used to improve the surface finish of gear teeth and extend the gear's life. The main benefits of gear grinding are:
1. Smoother Surface Finish: Gear grinding produces a much smoother surface finish than other methods such as milling or turning. This is important for reducing noise and vibration, and improving the efficiency of the gear.
2. Increased Gear Life: The increased accuracy and smoothness of the gears produced by gear grinding can lead to a significant increase in the life of the gear. In some cases, gear grindings have been known to more than double the lifespan of gears.
3. Greater Efficiency: The increased accuracy and smoothness of gears produced by gear grinding also lead to greater efficiency in power transmission. This can save energy and reduce costs in many applications.
Common Types of Gears
There are several common types of gear that are used in a variety of applications. Some of the most popular types of gear include:
-Spur gears: Spur gears are the most common type of gear and are used in a wide range of applications. Spur gears have straight teeth and are used to transmit rotational motion between parallel shafts.
-Helical gears: Helical gears have teeth that are angled relative to the axis of rotation and can transmit rotational motion between non-parallel shafts.
-Bevel gears: Bevel gears have conical-shaped teeth and are used to transmit rotational motion between intersecting shafts.
-Worm gears: Worm gears have spiral-shaped teeth and are used to transmit rotational motion between non-intersecting shafts.
The Use of CNC Machining in Gear Grinding
CNC machining is a process that uses computer-controlled machines to remove material from a workpiece. The process is typically used to create parts with complex shapes or features that would be difficult to machine using traditional methods.
CNC machines can be used for a variety of applications, including gear grinding. Gear grinding is a process that removes material from the surface of a gear to improve its tooth profile or surface finish. It can also be used to create gears with special shapes or features, such as spiral-cut gears.
There are several advantages of CNC machining for gear grinding:
-First, it is a very precise process that can produce highly accurate results.
-Second, it is relatively fast and efficient, which makes it an ideal choice for high-volume production runs.
-Finally, CNC machines can be used to grind a variety of materials, including metals, plastics, and composites.
CNC Machining at True Gear & Spline Ltd.
You can rely on us at True Gear & Spline Ltd. for your gear grinding needs. We use the latest CNC machines to ensure nothing but the best gears and splines for our clients. We boast Kapp Niles ZP 12 CNC gear grinding machine that produces ground gears up to 1250 mm diameter and 1000 mm face width. Be it spur, helical, double helical, or crowned gears, our effective CNC machining service guarantees that all our gears meet the highest standards. The Kapp Niles ZP 12 combined with advanced CNC gear grinding software make us one of the best gear manufacturers in Ontario.
Conclusion
Gear grinding is a process that can be used to produce gears with very precise profiles, shapes and sizes. It is an efficient and cost-effective way of producing high-quality gear components for a variety of applications. The advantages offered by gear grinding make it desirable for many industries, including automotive, aerospace and medical equipment manufacturing. No matter what industry you belong to, you can depend on us at True Gear & Spline Ltd. for all your gear manufacturing, gear shaping, and gear grinding needs. Our CNC machining services are unmatched. Call us today to learn about everything we can do for you.