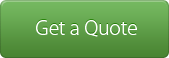
Sleeve Coupling
Sleeve coupling is a popular solution for engineering and manufacturing applications. It is most commonly used to transmit power and torque between two connecting shafts. The main goal of implementing a sleeve coupling is to counter any misalignments that may occur due to shock or vibration. Simply put, a sleeve coupling comprises a cylindrical sleeve that connects two shafts.
The simple design of these couplings allows one to accommodate different types of misalignments such as angular, parallel, and axial. Therefore, sleeve coupling is a versatile solution for many mechanical problems plaguing the engineering and machinery sectors.
Features and Major Advantages of Sleeve Couplings
Sleeve couplings offer a plethora of advantages:
Misalignment Tolerance: Sleeve couplings are built to withstand slight misalignments between two shafts, be they angular, parallel or axial. The level of tolerance depends on the type of sleeve coupling.
Cost-Effectiveness: It is a relatively simple and reliable solution to tackle issues such as misalignment. Since it is not very expensive to manufacture and install, it is quite cost-effective in the long run.
Effective Vibration Damping: Errant vibrations and shocks can lead to misalignment and damage to the equipment. Sleeve coupling effectively tackles this issue.
Simplistic Design: Featuring mainly a cylinder or sleeve and associated fasteners, sleeve coupling is known for its simplistic and practical design. This also makes it easier to install between two shafts requiring vibration damping or misalignment reduction.
Low Maintenance: Although dependent on the type, most sleeve couplings are considered low maintenance and require some lubrication at best from time to time.
Applications of Sleeve Couplings
With its simple yet effective design, this versatile solution is employed by numerous industries such as:
Manufacturing Sector
Pumps and compressors are an integral part of many manufacturing sectors. Here’s how sleeve coupling aids in their optimal functioning:
Pumps: Sleeve coupling connects the motor and pump shafts, making it highly useful in water, chemical and other types of specialized pumps.
Compressors: Power transmission is a major concern in compressors. Sleeve couplings help execute this properly by transmitting power from the main motor to the compressor shaft.
Material Handling
Conveyor systems, a pillar of the material handling sector, employ sleeve coupling to connect the drive motor to the conveyor shafts. This coupling helps in the smooth movement of the conveyor and effective material handling.
Automotive Sector
Sleeve coupling is used to connect the engine to the vehicle's numerous mechanical components. This makes it a staple in heavy-duty automotive equipment. It is also found extensively in gearboxes.
Agricultural Sector
In the farming and agricultural sectors, sleeve coupling is an integral part of tractors, mixers, and agitators.
Marine Sector
The propeller shaft plays a key role in marine locomotion. Sleeve coupling enables a smooth connection between the engine and the propeller shaft.
Why Choose Sleeve Couplings?
Sleeve couplings are variously used across multiple industries as they help counteract the effects of vibration and shock which are inevitable in all the above-mentioned applications. Therefore, some degree of misalignment is also to be expected. However, irrespective of the nature of the misalignment, sleeve coupling ensures seamless operation.
How Sleeve Couplings Work
The operation of a sleeve coupling is relatively simple. The torque and power are transmitted from one shaft to another via the coupling. The two shafts connected by the coupling are the driving shaft and the driven shaft, respectively. When the driving shaft is set in motion, the mechanical coupling transfers this motion to the driven shaft, thereby completing a cycle of transmission. For optimal torque transmission, the sleeve coupling is designed in such a way that it creates a good amount of friction between the sleeve and the shafts. To prevent slippage, the sleeve is combined with keys and keyways.
Types of Sleeve Couplings
Rigid Sleeve Coupling: This type of sleeve coupling is used when precise shaft alignment is possible. Even the smallest of misalignments can cause problems in rigid sleeve coupling. Apart from requiring precise alignment, it is also known for its high torque transmission capabilities.
Flexible Sleeve Coupling: In cases where shaft alignment is not perfect, flexible sleeve coupling can be used. They offer a degree of freedom with misalignment and help reduce shock and vibrations.
Muff Sleeve Coupling: A form of rigid sleeve coupling, it uses a hollow cylinder which is placed and removed over the two connecting shafts with the help of a key.
Operating Design Considerations Of Sleeve Coupling
As discussed above, a sleeve coupling operates by transmitting the motion of the driving shaft to the driven shaft via friction. Now, here are some key factors we consider when choosing a sleeve coupling for your particular operation:
Material Selection: Sleeve couplings can be made from a wide variety of materials such as steel, aluminum, polymer, bronze, composites, and more.
Dimensions And Tolerances: In terms of dimensions, the diameter and lengths of the shaft are key to consider. As for tolerances, it refers mainly to any possible misalignment that may occur. If it is significant, it is best to opt for a flexible sleeve coupling instead of a rigid sleeve coupling.
Environmental Factors: The presence of dust, moisture, and adverse temperatures might also dictate the design of a sleeve coupling.
Contact Us:
True Gear & Spline Ltd. offers top-notch flexible and rigid sleeve coupling and their variations. For questions about our sleeve couplings, or to place an order for our quality products, reach out to us directly at 519-653-1301.
Frequently Asked Questions:
1. What types of steel are typically used in a sleeve coupling?
A sleeve coupling generally uses a form of carbon steel, stainless steel, or a specified alloy depending on the strength required and environmental factors.
2. Why is steel a popular material for designing sleeve coupling?
The widespread use of a variety of steel can be attributed to its durability in handling high torque, a key factor when selecting a sleeve coupling.
3. Do sleeve couplings fail, and if so, what are the most probable causes?
Yes, sleeve coupling is susceptible to failure like any equipment. However, the causes can almost always be attributed to improper selection. For instance, the sleeve selected is not compatible with the misalignment in the shaft, or it has not been lubricated properly. Lastly, the sleeve coupling might not be suitable for a particular environmental condition, requiring some additional modifications or the need to choose a different coupling altogether.