Keep up to date with us on the latest industry news as well as what's going on at True Gear & Spline Ltd. We also post articles for insider tips and tricks, so make sure to check back frequently.
The Art of Bevel Gear Cutting
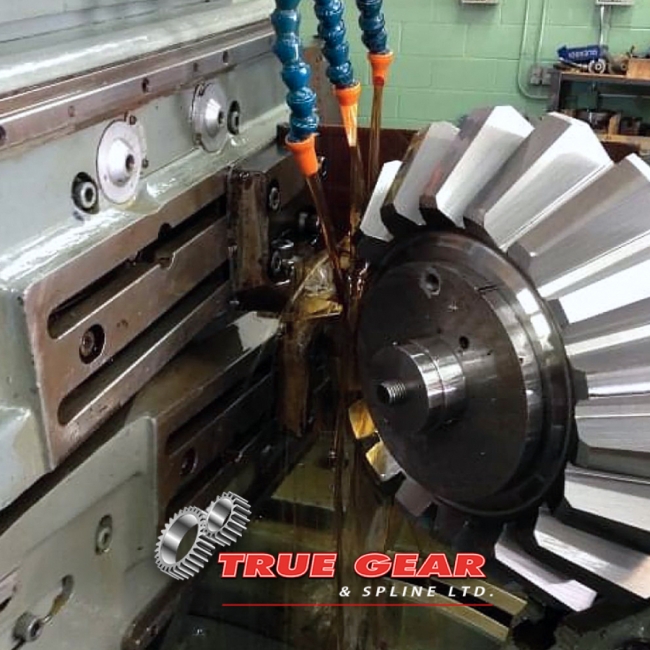
While spur gears are often celebrated as the most effective gear, people often tend to forget just how awesome bevel gears are. These specialized gears with oblique tooth-bearing surfaces facilitate power transmission between intersecting shafts at different angles. While most gears are cylindrical, bevel-type gears have conical surfaces. Gear manufacturers, depending on the needs of their customers, cut teeth onto the conical surfaces.
The unique design enables these gears to facilitate torque between two mechanical components smoothly and efficiently. The mechanical prowess of bevel-type gear makes it indispensable for various applications. Did you know? Bevel gears are found in everything from automobiles and helicopters to locomotives and cooling towers.
Everyone from large-scale industrial clients to individual business owners relies on True Gear & Spline Ltd. in Cambridge, ON. Our extensive facility is equipped with cutting-edge technology, allowing us to offer flawless gear manufacturing services to our clients. If you have ever wondered how bevel gears are manufactured, read this blog until the end.
Advantages of Bevel Gears
Ideal For Application With Space Constraints
Bevel gear is a versatile and widely used gear in various industries. The ability of these gears to transmit power between intersecting shafts at different angles is extraordinary and unmatched. Bevel-type gears are apt for applications with limited space.
Ability to Handle High Loads
The primary objective of gears is to facilitate torque transfer between mechanical components. To do so, the gear must be able to handle high loads without breaking or being damaged. One of the most significant advantages of bevel gear is its ability to handle high loads and operate at high speeds. The teeth on the conical surface of bevel-type gears are designed to ensure maximum efficiency while generating minimal noise.
Flexibility
It is one of the most important advantages of bevel gears. Custom gear manufacturers can produce gears with countless design variations. Gears with different tooth profiles are suitable for different applications. Straight-cut bevels are used for automobile differential gear systems meanwhile spiral bevels are a crucial part of helicopters.
Understanding The Art of Bevel Gear Cutting
Gear cutting is an intricate process that involves many nuances. Gear manufacturers leverage the power of cutting-edge technology to produce custom gears with precise tolerances. The use of CNC machining is a common practice in the industry. Sophisticated gear-cutting CNC machines speed up the entire process and help improve efficiency among gear manufacturers. True Gear & Spline Ltd. is a gear manufacturer based in Cambridge, ON.
We extend our bevel gear-cutting service to clients across Toronto, GTA, and other regions in Ontario. We are proud owners of Gleason Coniflex gear generators which we use to offer flawless gear cutting services. We own two Gleason gear cutters, the 2A and 24A respectively. While the former can cut a .25" gear, the latter can cut a .35" diameter bevel gear with precision.
Thanks to our sophisticated machinery and skilled employees, we can custom-produce all types of bevel gears while meeting the highest standards. With quick turnaround time, precise tolerance, and the ability to manage orders of all sizes, we offer complete turnkey solutions to our clients.
Common Challenges and Solutions in Bevel Gear Cutting
Challenge #1: Achieving Precision
Owing to the complex shape geometry of bevel gears, achieving precision can be tricky. The margin for error is minimal in gear manufacturing. This means that even the slightest deviation can lead to inaccurate tooth profiles and incorrect angles.
Solution
The introduction of CNC machining in the gear-cutting process solves this dilemma. An experienced gear manufacturer can significantly benefit from CNC machining. With the help of software, the operator can control variables like feed rates and tool positioning, thus achieving precision.
Challenge #2: Maintaining Consistency in Quality
Ensuring consistent quality is a huge challenge for gear manufacturers, especially while handling larger orders. It is easy to get confused between the dimensions requested by different clients if orders are being run simultaneously.
Solution
Putting in place rigorous quality control measures is the easiest solution to this problem. By introducing quality checks at every stage of the manufacturing process, gear manufacturers can avoid inconsistency in quality. True Gear & Spline Ltd. has in place foolproof quality checks to guarantee no gear leaves our floor with any flaws whatsoever.
Conclusion
You can rely on True Gear & Spline Ltd. for all your bevel gear-cutting needs. We custom produce and supply gears with precise tolerances. We leverage the power of cutting-edge technology and experienced employees to successfully manufacture all types of gears. What's more? We also offer services like gear hobbing, gear grinding, and gear shaping at the best rates. Call us today to learn about all we can do for you.