Keep up to date with us on the latest industry news as well as what's going on at True Gear & Spline Ltd. We also post articles for insider tips and tricks, so make sure to check back frequently.
The Nuances of Bevel Gear Cutting
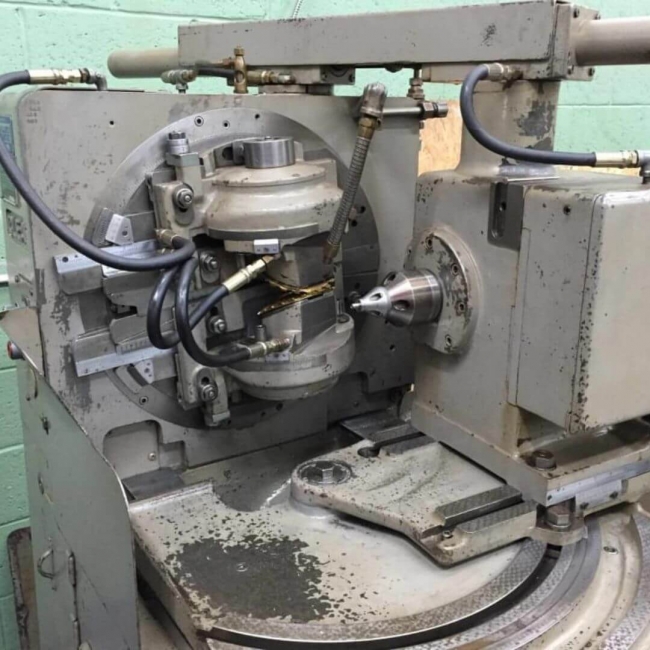
What might sound like an easy process is in fact extremely demanding. We are talking about gear manufacturing, a fascinating process that requires precision, skill, and attention to detail. There are different types of gear used by industries. Spur, helical, ground, gear, and internal are some of the most common gears. Each gear type is manufactured using a dedicated process. Grinding, shaping, machining, and slotting are all techniques used by gear manufacturers to achieve perfection. While one method works for a particular gear type, it won't for the other. In today's blog, we talk we specifically discuss the bevel gear-cutting process. Bevel-type gears are conically shaped, thus making its manufacturing a rather difficult affair. Read this blog until the end to learn the nuances of bevel gear cutting.
The Intricacies of Bevel Gear Cutting
Bevel gear cutting is a highly intricate process that involves precision, skill, and advanced machinery. This specialized cutting technique is used to create bevel gears - gears with cone-shaped teeth that are designed to transmit power between intersecting shafts.
Selecting the right cutter is the most crucial step in gear cutting. Any gear manufacturer worth their salt understands the importance of investing in a sophisticated gear cutter. True Gear & Spline Ltd. boasts a Gleason Coniflex gear generator. This machinery is capable of cutting bevel-type gears with a diameter of .25" to .35" with the utmost precision. The combination of world-class gear cutters and expert gear manufacturers allows us to manufacture custom gears with precise tolerances.
Apart from the selection of gear cutters, there are other nuances involved in gear cutting. Making sure the mounting distance is accurate is a crucial aspect of gear cutting. Mounting distance is a crucial factor that determines the efficiency of gears. Verifying backlash is another nuance involved in bevel gear cutting. One of the key challenges in gear cutting is achieving accurate tooth profiles and smooth surface finishes. Any deviations or imperfections can lead to poor performance or premature failure of gears in service.
Conclusion
As we have seen in this blog, there are several nuances involved in bevel gear-cutting. A task with so many intricacies involved should be left to the experts. True Gear & Spline Ltd. is a leading manufacturer of custom gears in Ontario. We rely on CNC machining gear and splines with precise tolerances. Reach out to our team to learn about everything we can do for you.