Keep up to date with us on the latest industry news as well as what's going on at True Gear & Spline Ltd. We also post articles for insider tips and tricks, so make sure to check back frequently.
Top 5 CNC Machining Trends That Will Drive Success In 2023
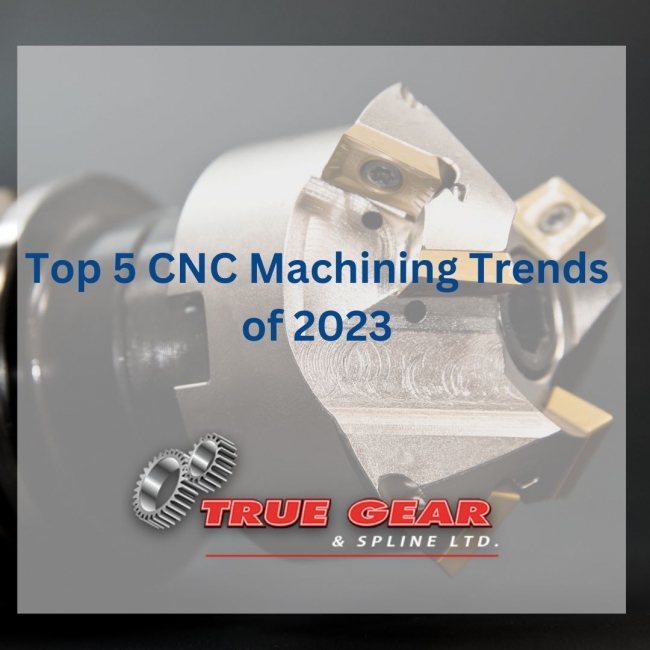
CNC machining has revolutionized the manufacturing industry, and its impact is only growing at a steady rate. As technology progresses at an unprecedented pace, we are witnessing new trends emerge that promise to drive success for businesses that embrace them. From AI and machine learning to multi-axis machines and advanced software, these innovations are unlocking new possibilities for CNC machining services. In this article, we'll explore the top CNC machining trends that will shape the future of manufacturing in 2023 and beyond.
5 CNC Machining Trends That Will Drive Success in 2023
1. Greater Use of AI and Machine Learning:
- The manufacturing industry is constantly evolving, and one of the key trends that will shape CNC machining in 2023 is the greater use of AI and machine learning. Artificial intelligence has already transformed several industries, and its impact on CNC machining will be no different. It has broadened the advantages of CNC machining.
- AI technology allows for more accurate data analysis, which leads to better decision-making in terms of tool selection, cutting parameters, and feed rates. Machine learning algorithms can adapt to new environments, improve efficiency by reducing cycle times and optimize the entire process from design to production. This results in better accuracy and precision with minimal human intervention or conventional machining.
- Machines equipped with AI-powered sensors are capable of detecting any anomalies or errors that may occur during a job run. This helps manufacturers identify issues before they escalate into significant problems that could cause expensive downtime or damage equipment.
- The benefits don't stop there. AI also enables predictive maintenance schedules based on real-time machine performance data. These insights help schedule maintenance activities proactively rather than reactively - resulting in increased uptime while extending the life span of machines.
2. Integration of 3D Printing and CNC Machining:
- The integration of 3D printing and CNC machining has been an exciting development in the manufacturing industry. By combining these two technologies, manufacturers can benefit from the accuracy and precision of CNC machining while taking advantage of the flexibility offered by 3D printing.
- One major advantage is that it allows quick prototyping. With a 3D printer, designers can quickly create a prototype to test their ideas before committing to full-scale production using CNC machines. This can save time and money in the long run as it helps identify design flaws early on.
- Another advantage is that it enables customization on demand. Using both technologies together, manufacturers can produce custom parts or products with greater ease than ever before. They simply need to modify their designs using CAD software and then print them out using a 3D printer followed by finishing touches with CNC machining.
- Integrating these two technologies streamlines production processes significantly by reducing material waste and speeding up lead times. The ability to quickly switch between rapid prototyping via 3D printing and mass-producing final products through CNC machining offers great potential for increased productivity for a CNC workstation.
3. Increased Adoption of Automation and Robotics:
- One of the biggest advantages of using automation and robotics in CNC machining is the ability to reduce manual labour. These machines can perform tasks that would otherwise require skilled personnel. Thus, freeing up workers for more complex or creative tasks.
- Automation and robotics can significantly improve accuracy and speed in CNC machining services and operations. They can work consistently without breaks or fatigue, ensuring high-quality results every time.
- These machines can also enhance safety by reducing the risk of accidents caused by human error. With fewer workers operating machinery on the shop floor, there are fewer opportunities for mistakes or injuries to occur. As technology continues to advance, we can expect even greater levels of integration between CNC machining and automation/robotics.
- From automated inspection systems to collaborative robots working alongside humans on the shop floor, this trend has immense potential for driving success in manufacturing industries across various sectors.
4. Advanced Software:
- Advanced Software has been a driving force behind the success of CNC machining. The use of computer-aided design (CAD) and computer-aided manufacturing (CAM) software has revolutionized the way CNC machines are programmed and operated. Advanced software helps manufacturers create more complex designs with greater precision and accuracy. These programs allow quick changes in designs without having to reprogram entire processes from scratch.
- Advanced software also provides real-time monitoring of production processes that enable manufacturers to make adjustments on-the-fly, reducing errors and increasing efficiency. This not only saves time but also reduces costs associated with material waste. It also facilitates better communication between different departments like designing, engineering, programming etc., making teamwork much easier than before.
- As technology advances at an exponential rate so does the CNC machining industry evolve along with it. Advanced software is just one example of how innovation is helping companies optimize their production process while ultimately achieving higher levels of success.
5. Advancements in Multi-Axis Machining
- Advancements in multi-axis machining have been a game-changer for the manufacturing industry. With traditional CNC machines capable of only three axes of movement, multi-axis machines like 5-axis CNC machining add more flexibility and precision to the process.
- One significant advantage of multi-axis machining is its ability to produce complex shapes and parts with greater accuracy. By adding more axes, manufacturers can create intricate features that would be impossible using conventional methods.
- Another benefit of multi-axis machining like a 5-axis CNC machining is speed. With multiple tools working simultaneously, production times are significantly reduced compared to single-axis machines.
- This efficiency translates into cost savings for manufacturers. These advancements allow manufacturers to work with a broader range of materials such as hardened steels and titanium alloys which were previously difficult or impossible due to their hardness.
- Advancements in multi-axis machining provide an array of benefits including increased accuracy, faster production times and expanded material capabilities. It's no surprise that this trend will continue driving success in 2023 for those who adopt it early on.
Conclusion
The CNC machining industry is constantly evolving and improving. With new technology advancements emerging every year, it's essential to stay up-to-date with the latest trends to remain competitive. We at True Gear & Spline Ltd. have been using CNC machining to offer a wide range of services including gear shaping, gear hobbing, and gear grinding. This advanced technology also helps us offer a wide range of gears like spur, helical, bevel, and ground with tight tolerances. We are one of the leading gear manufacturers in Ontario. Contact us today to learn about everything we can do for you.