Keep up to date with us on the latest industry news as well as what's going on at True Gear & Spline Ltd. We also post articles for insider tips and tricks, so make sure to check back frequently.
A Guide To Understanding Gear Manufacturing Processes
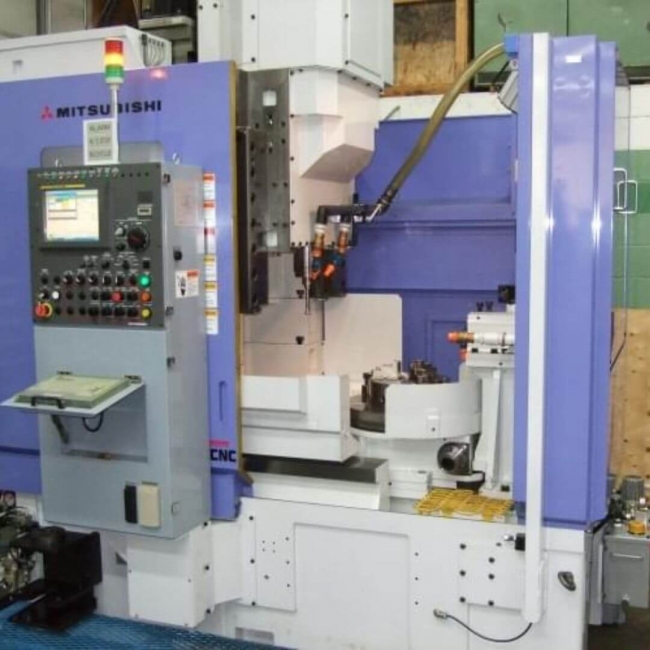
Gears power everything from small clocks to heavy-duty industrial machinery. The ability of gears to transmit torque is commendable. This ability makes gears an integral part of mechanical systems across industries. These mechanical devices enable you to do everything from driving a car to using escalators. Given the importance of gears, the gear manufacturing process needs to be planned meticulously. Any discrepancy in the gear production process can have far-reaching effects. Have you ever wondered what goes into the production of gears? This blog discusses exactly that. We discuss in this comprehensive guide the different types of production processes used by gear manufacturers.
Common Gear Manufacturing Processes
There are many different types of gears. Each type is suitable for specific applications. Custom gear manufacturers rely on a wide range of gear manufacturing processes. Each process is suitable for a specific gear type. We list below a few gear manufacturing processes.
Casting
This process involves pouring molten metal into a mould with the desired gear shape. Casting is a common technique used to produce flawless gear blanks. A gear blank is the metal base or the disc on which teeth are cut depending on the client's requirement. Once the blank has been created through casting, gear manufacturers rely on machining to cut teeth onto it.
Forging
As the name suggests, in this process gear blanks are forged into perfection. This process uses heat treatment and the application of pressure to shape the blanks. A heated piece of metal is shaped with the help of dies or hammers. Thanks to the resultant fatigue properties, forging is ideal for producing strong and durable gears.
Blanking
It is a rather simple process where cutting tools are used to produce gear blanks. Dies are often the cutting tool of choice for blanking. With the help of dies, sheet metals are cut into the desired shape and size rather quickly. Blanking is most commonly used to produce top-notch spur gears.
Gear Machining
Gear machining, a general term, encompasses multiple techniques. CNC machining is commonly used by modern gear manufacturers. CNC machining allows gear manufacturers to produce custom gears with precise tolerances. Below are some of the most popular machining processes.
Hobbing
Spur and helical are the most commonly used gears. Gear hobbing is an apt technique for manufacturing spur and helical gears. This technique gets its name because of the "hob" tool. It is a specialized tool that removes bits of the workpiece until the desired result is achieved. CNC gear hobs guarantee precision and quick turnaround time.
Shaping
Gear shapers are equipped with different types of cutters like helical, shank, hub, and disc. In gear shaping, a toothed cutter is meshed with a gear blank placed on a different shaft. The rotating cutter keeps gnawing into the gear blank, eventually achieving the desired shape. Gear shaping is a gear production process used to manufacture internal and external gears. The versatility of this technique makes it possible to produce flawless double helical gears and involute splines with ease.
Broaching
A broach is a cutting tool with teeth. Broaching is one of the quickest machining techniques in gear manufacturing. The increasing tooth size in a broach enables precise gear cutting. What's more? This technique is apt for even machining multiple gear blanks in one go. Linear and rotational are the two main types of broaching.
Milling
CNC milling has proven to be a game changer for gear manufacturers. The efficiency and turnaround time of CNC milling machines is unmatched. The use of rotary cutters is a prevalent practice in milling. In milling, the workpiece stays stationary while the cutter is advanced toward it. Milling is widely used for creating spur gears, bevel gears, and worm gears, among others.
Gear Machining Post Processes
While the above-mentioned processes are crucial for manufacturing gears, they are not enough Achieving finishing is crucial to ensure the optimal performance of gears. Gear manufacturers rely on a wide range of post processes to ensure flawless finishing. Following are some post-gear machining processes that refine and enhance the gear's performance.
Gear Grinding
In this post-process, a grinding wheel is used to polish the gears to perfection. The grinding wheel removes excess material from the gear to achieve precise tooth profiles and dimensions. The grinding wheel produces a fine surface finish, resulting in low-noise operation and increased durability.
Lapping
A lapping tool does a great job of chipping away unwanted material from gears. The lapping tool is also perfect for polishing gears that need to be able to run silently. It involves rubbing abrasive particles against the gear's surface, removing any irregularities or roughness left after machining.
Honing
While grinding and lapping are more apt for external gears, honing is often used to polish internal gears. Honing is a preferred post-process to guarantee an accurate tooth profile. What's more? Honing also helps improve surface integrity.
Conclusion
As we have seen in this blog, gear manufacturing is an intricate process that requires access to sophisticated machinery. Owing to the nuances involved in gear production, it should be left to the experts. True Gear & Spline Ltd. is a leading manufacturer of custom gears and splines. We use state-of-the-art machinery and equipment to manufacture spur, helical, worm, and ground gears, among many others. We also boast the capability to manufacture splined shafts with precise tolerances. From CNC gear shaping and cutting to keyway slotting and broaching, no matter what you are looking for, we have got you covered. Get in touch with us today to learn about all we can do for you.