Keep up to date with us on the latest industry news as well as what's going on at True Gear & Spline Ltd. We also post articles for insider tips and tricks, so make sure to check back frequently.
The 3 Essential Methods of Gear Machining
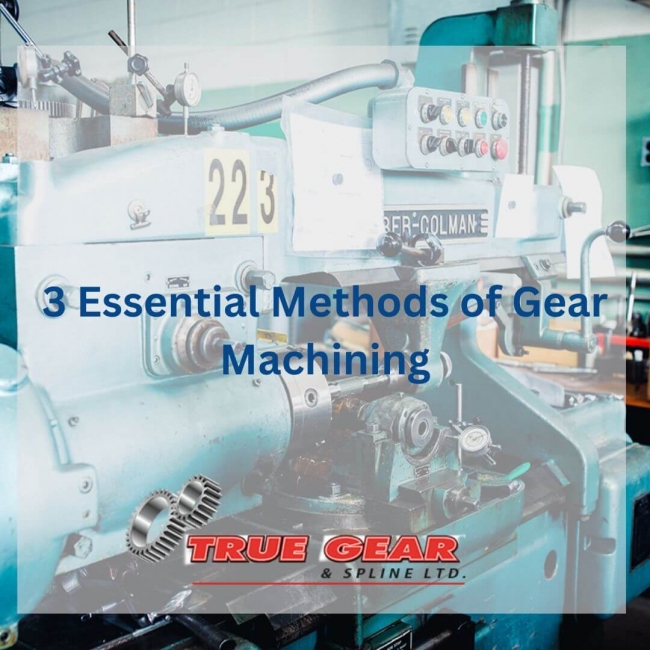
Gears are crucial for the functioning of mechanical systems across industrial setups. Imagine a world without gears. All the manufacturing and industrial units would come to a halt and the losses would be unfathomable. Simple in design yet highly effective in transferring torques, there is no replacement for gears. It can be argued that the simple yet effective design is what makes gears irreplaceable. However, the design of gears tricks you into believing that gear manufacturing is a fairly simple process. This cannot be farther from the truth. Gear manufacturing is an intricate process that involves state-of-the-art tools and machinery. Machining is an inextricable part of gear manufacturing. While there are various methods of gear machining, we focus mainly on three — Gear generation, gear shaping, and gear hobbling.
Three Essential Gear Machining Methods Are As Follows
1. Gear Generation
Gear generation involves the use of sophisticated cutting tools like rack cutters. This is often the first step in manufacturing machined gears. There are different methods of producing machined gears. We list below some of the most common ones:
- The Sunderland Method is an important aspect of gear generation. It is used for producing larger gears in a very precise manner. It involves two distinctive cuts where one is for roughing the gear tooth while another cut provides finishing touches. The Sunderland Method makes use of a rack-type cutter. This cutter reciprocates the machining action while a second rolling-type cutter interacts with the blank. Both the cutters work like a pair of racks and pinions, ensuring higher accuracy.
- Gear shaping is a process used for cutting teeth on a gear blank using a sophisticated cutter. One of the most common machined gear generation methods, gear shaping is used to produce teeth on an external or internal gear by generating straight-sided splines or involute form profiles. This process is ideal for manufacturing of gears such as helical and spur.
- Gear hobbing involves using a specialized tool called a hob which rotates at high speed against the workpiece's surface creating precisely cut teeth. It's perfect for the mass production of cylindrical components like shafts and gears. The use of CNC hobbing machines is prevalent among trusted gear manufacturers worldwide.
2. Gear Form Cutting
Gear form cutting is one of the essential methods in gear machining. It involves shaping gears by removing excess material from a blank piece using various machines.
Milling is one of the most common types of gear form cutting. In gear milling, a sophisticated machine removes material by rotating at high speeds while making contact with the gear. CNC machines are preferred by gear manufacturers for milling owing to their high efficiency and ease of operation.
Another method of gear cutting that's often used is electrical discharge machining (EDM). The process uses an electrode to remove material from a conductive surface that's placed in close proximity to it. This results in incredibly accurate cuts, making EDM perfect for producing intricate gears.
Planing and slotting are also popular forms of gear cutting. Planing machines use a linear reciprocating motion to move their tools across the workpiece, creating flat surfaces or grooves on them as needed. Slotting machines, on the other hand, create slots by removing material along specific lines. The combination of planing and slotting results in industrial-grade gears.
3. Gear Forming
When it comes to gear forming, there are three essential methods that manufacturers can use: rolling, casting and powder metallurgy. Each method has its own unique advantages and disadvantages depending on the specific requirements of the project.
- Rolling is a popular choice for producing large quantities of gears with high precision at a low cost. This process involves pressing the metal between two rollers until it takes on the desired shape. The resulting gears have excellent strength and durability, making them ideal for heavy-duty applications.
- Casting is a method for gear forming where molten metal is poured into a mould and left to cool before being removed from the mould. This technique produces gears with complex shapes that would be difficult or impossible to produce using other methods. However, casted gears may have lower dimensional accuracy than those produced by other techniques.
- Powder metallurgy involves compressing powdered metal in a die under high pressure to form intricate shapes such as gears. The process also allows manufacturers to create parts with different properties by adding alloying elements to the mix during compaction.
Trust True Gear & Spline Ltd. For All Your Gear Machining Needs
When it comes to gear machining, finding a reliable and experienced company is essential. True Gear & Spline Ltd. has been providing top-quality gear manufacturing services for almost five decades.
Our team of experts specializes in all types of gear machining, including gear shaping, hobbing, milling and more. Our quality check is on-point and stringent, ensuring that all the gears and splines we manufacture meet the highest standards. The combined experience of our staff is what makes us stand out from the rest of our competitors. Through our decades of experience in manufacturing gears, we have handled projects of all types.
Our continued success is a reflection of our commitment to customer satisfaction and excellence. Our extensive 22,000-square-foot facility in Cambridge, ON is equipped with state-of-the-art equipment and CNC machines. Whether you need custom gears or a high-volume production run, True Gear & Spline Ltd. has the capabilities to meet your needs on time and within budget. Contact us to discuss your gear manufacturing needs today.