Keep up to date with us on the latest industry news as well as what's going on at True Gear & Spline Ltd. We also post articles for insider tips and tricks, so make sure to check back frequently.
The Art of Spur Gear Manufacturing
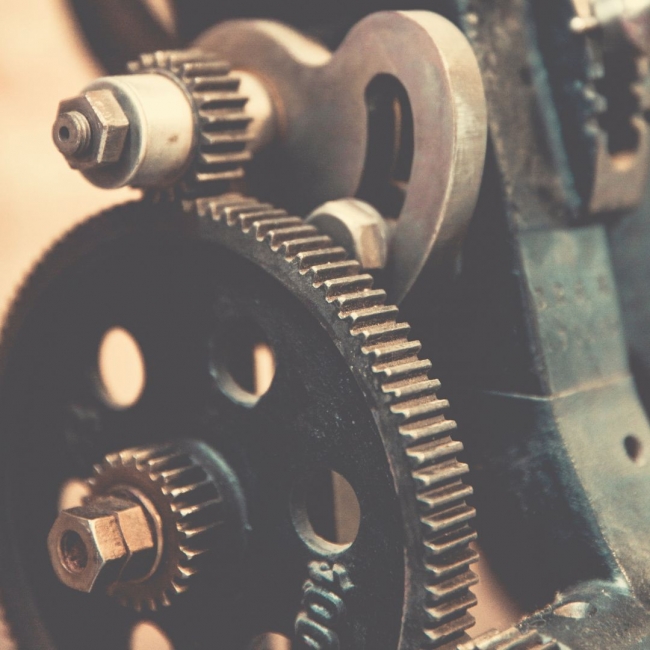
Looking for a gear that can withstand the test of time? Look no further than spur gears. These versatile and durable components have been used in everything from automobiles to industrial machinery, making them a critical part of modern manufacturing. But what goes into making these powerful gears? In this post, we'll dive deep into the art of spur gear manufacturing.
Designing Spur Gears
They are typically designed for high-speed and/or heavy-duty applications. The teeth are cut at a precise angle to ensure proper engagement and prevent slipping. The gear teeth also have a specific profile that helps to minimize noise and vibration.
There are a few things to consider when designing spur gears, such as material selection, tooth form, dimensional tolerances, etc. Some common materials used for these gears include steel, bronze, and plastic. It's important to select a material that is compatible with the operating conditions (temperature, load, speed, etc.) and will not cause excessive wear on the mating surfaces.
The tooth form is another important consideration when designing these gears. The shape of the teeth affects the strength, durability, and accuracy of the gear. There are many different tooth forms available, so it's important to select one that is best suited for the application.
Dimensional tolerances are also critical when manufacturing spur gears. The gear must be machined within very tight tolerances to ensure proper engagement with the mating surface. If the tolerances are too loose, there will be excessive
The Manufacturing Process
The gear manufacturing process can be divided into three main steps: cutting, grinding and lapping.
Cutting is the first step in the manufacturing process and is typically done using a computer numerical control (CNC) machine. The CNC machine is programmed to cut the gears to the desired shape and size.
Grinding is the next step in the process and is used to smooth out the rough edges of the gear teeth from the cutting step. Lapping is the final step in the manufacturing process and is used to create a smooth, polished surface on the gear teeth.
Conclusion
As you can see, there’s a lot that goes into the art of spur gear manufacturing. It requires precise measurements and techniques to ensure proper fitment. If you are ever in need of an expert spur gear manufacturer, you can rely on us at True Gear & Spline Ltd. We are one of the leading splined shaft and gear manufacturers in Ontario. Call us today to learn about everything we can do for you.