Keep up to date with us on the latest industry news as well as what's going on at True Gear & Spline Ltd. We also post articles for insider tips and tricks, so make sure to check back frequently.
Torque Transmission Best Practices for OEM Engineers
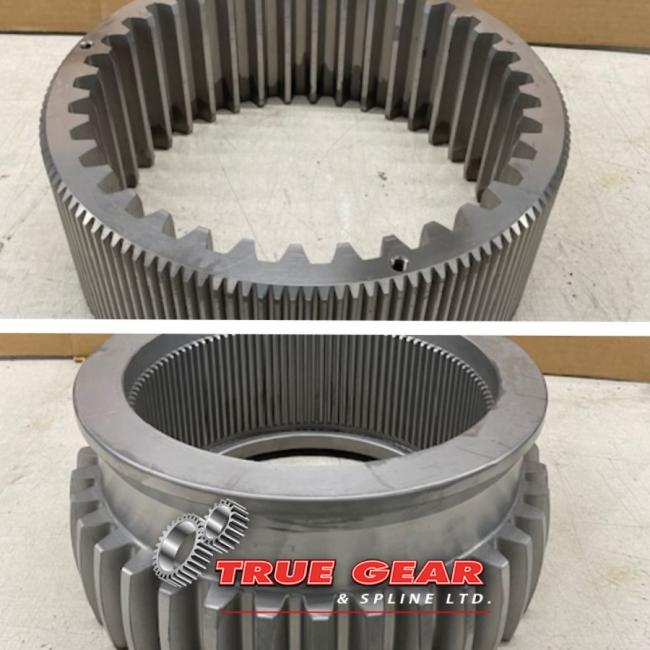
Introduction: Why Torque Transmission Matters for OEMs
Role of Torque In Power Delivery
Torque transmission is directly related to power delivery among mechanical components. In the OEM industry, torque plays an inextricable role. It is responsible for determining factors such as initial acceleration, load-bearing capacity, and the overall performance of mechanical components.
Why Engineers Can't Afford Missteps in Torque Planning
If you are an engineer in the OEM industry, the margin for error is next to none. Missteps must be avoided at all costs to prevent downtimes and damage to components or equipment. Since torque transmission is the backbone of operations, getting it right is sacrosanct. To reiterate, the success of the entire operation will depend on that.
Overview
We write this guide to discuss torque transmission best practices for OEM engineers. Topics such as torque transmission fundamentals and challenges will be touched upon. You can also read about situations that call for custom torque transmission components. This is the ultimate guide for OEM engineers dealing with torque transmission.
Understanding Torque Transmission Fundamentals
What Is Torque and How Is It Transmitted?
Torque transmission is merely the transfer of rotational force between mechanical components. It is the rotational equivalent of linear force. Gears, splined shafts, couplings, clutches, belts, and chains are primarily used to facilitate torque transmission. Without torque, engines cannot power vehicles or industrial machinery.
Key Factors That Impact Torque Transfer Efficiency
Material Selection
The components used for torque transmission must be strong enough to handle the load. A low-strength material will break and fail to transmit torque. It is imperative to source torque transmission components from trusted manufacturers to ensure seamless operations.
Gear & Shaft Alignment
Misalignments are detrimental to effective torque transfer. As an OEM engineer, you must prevent misalignments at all costs. Gear and sleeve couplings offer an effective solution against misalignments between gears and shafts. Loss of energy, damaged components, overheating, and premature wear and tear are problems caused by inaccurate gear and shaft alignment.
Load Variations
Inconsistent or poor power supply often causes load variations. The use of torque limiters is recommended to keep the load variations in check. Non-stop variations increase the slippage of torque transmission components. An effective load-sharing strategy and appropriate lubrication also help control damage caused by load variations.
Common Torque Transmission Challenges in OEM Applications
Misalignment and Wear Over Time
Even the best torque transmission component will experience wear and tear over time. The pace of wear and tear largely depends on factors like frequency of usage, material strength, and quality of maintenance practices. An OEM engineer must regularly inspect torque transmission components for signs of wear and tear. Once beyond redemption, the components must be replaced to ensure smooth operations.
Inconsistent Load Handling
Torque transmission systems often must deal with varying loads. Instability, vibration, and failure of components are side effects of inconsistent loads. Through periodic observations and research, OEM engineers must record the lowest and peak loads. They must then take necessary actions to ensure the torque transmission system can handle such loads. The use of torque limiters and overload clutches is highly recommended.
Poor Gearbox or Shaft Compatibility
Mismatched components are one of the primary challenges to achieving flawless torque transmission. All the components you use must be specifically designed for your torque transmission system. It is imperative to work with custom torque transmission component manufacturers to prevent gearbox or shaft incompatibility. Factors like dimensional tolerance, load capacity, and rotational speed must be considered while sourcing torque transmission components.
Engineering Best Practices for Reliable Torque Transmission
Step 1: Define Application Load Profiles Clearly
An engineer must fully understand the application load profiles before choosing components for seamless torque transmission. Without clearly defining application load profiles, the chances of investing in the wrong torque transmission components are high. Here are some factors to consider while defining application loads. Understanding the variables is essential to prepare the torque transfer system for real-life applications.
Average/Normal Load: Expected average load in ideal operational conditions.
Highest/Peak Load: The highest expected load the torque transfer system must endure.
Shock Load: Sudden spikes caused by voltage fluctuations, damage, or external factors.
Step 2: Choose Materials Based on Use Case
Material selection is one of the most important steps for OEM engineers. Wear resistance, fatigue strength, and even overall performance of torque transmission systems are influenced by this. Heredend steel and specialty alloys are commonly the material of choice.
Hardened Steel: Its unmatched strength and durability make it the go-to choice for torque transmission components such as gears, splined shafts, and couplings. Hardened steel components are ideal for high-torque applications.
Specialty Alloys: While hardened steel is preferred for common applications, specialty alloys are perfect for more nuanced operations. Specialty alloy components offer better resistance to corrosion, temperature and vibration. They are commonly used in the aerospace and marine industries.
Step 3: Apply Proper Surface Finishing and Heat Treatment
Gear Grinding: CNC gear grinding plays an important role in offering seamless torque transfer. Gear grinding helps the gears mesh better by refining the tooth surface. CNC gear grinding reduces micro-cracks and prolongs the life of torque transfer components.
Nitriding: This is a highly recommended surface treatment procedure for OEM manufacturers. It's called nitriding because nitrogen is diffused into the surface of steel. Nitriding improves strength and wear resistance.
Step 4: Optimize Gear Geometry for Torque Load Distribution
The geometry of the gear teeth affects how torque is transferred and how loads are distributed:
Helical vs Spur Gears: Helical and spur gears are similar. One of the most significant differences is the angle of the teeth. Spur gears have straight teeth; meanwhile, helical gears have teeth cut at an angle parallel to the axis of rotation. Helical gears are best suited for medium- to high-torque applications. Their gradual engagement works perfectly for such applications. However, spur gears are inexpensive and easier to manufacture. They do perfectly well in lower-speed applications.
Profile Modifications: Involute profile corrections, such as tip relief or crowning, help minimize stress concentrations and reduce noise and vibration. These tweaks can significantly enhance gear life under fluctuating loads.
Step 5: Follow Precise Machining Tolerances and Quality Checks
AGMA/DIN compliance: AGMA stands for American Gear Manufacturers Association, and DIN stands for Deutsches Institut für Normung, the German National Organization for Standardization. Adhering to the standards set by these prestigious organizations ensures precise machining tolerances and high-quality components.
In-Process Inspection: There must be a multi-layered quality check in place to ensure flawless quality. In-process quality checks must be in place to ensure perfection after each stage of production. CMM, gear analyzers, and laser scanning are helpful tools for in-process inspection.
When to Customize Torque Transmission Components
Generic gears and splined shafts might be suitable for certain tasks. This is where custom-designed components prove to be useful. If designed with proper planning, custom power transmission components ensure performance and reliability.
Situations That Demand Custom Gear or Shaft Design
High Torque With Limited Space
This scenario is common in the industrial world. Such a situation requires custom torque transmission components to get the job done. Off-the-shelf gears capable of transmitting higher torque are also often larger. It is impossible to use them in applications where space is a constraint. By working with a trusted gear and splined shaft manufacturer, you can control factors such as material selection, gear ratio, and tolerance.
Unique Coupling Requirements
Misalignments are quite common among torque transmission components. It is not always possible to achieve perfect alignment. Not to mention wear and tear, vibration, gearbox damage, and thermal expansion all lead to misalignment. This is where couplings come into play. Unique gear and sleeve couplings prevent angular and parallel misalignments.
Checklist: Why Should You Customize?
Unsure if you should get custom torque solutions? Here’s a checklist to help you make the right decision.
Standard Options Fail at Peak Torque
You must invest in custom components if your standard torque system is failing at peak torque. If the torque exceeds the peak levels, even briefly, you must consider custom gears and splined shafts. Using off-the-shelf components in such cases results in premature wear and tear and transmission failure.
The Load Profile is Inconsistent
Inconsistent loads are troublesome if your torque transmission system is not equipped to handle them. Custom components will help dampen shock, reinforce bearing interfaces, and efficiently manage backlash.
Environmental Extremes
Generic components might not do well under extreme conditions. They are prone to damage if exposed to high heat or extremely low temperatures. Exposure to abrasive substances and high-pressure underwater conditions also damages them. Custom components made of special alloys do well in such situations. They often have protective coatings to help them sustain and thrive in extreme environments.
A Retrofit is Needed in Legacy Equipment
If you rely on legacy equipment, finding replacement parts or components can be challenging. You can go for custom solutions in such instances. Custom replacements can modernize performance without a full redesign. For OEMs needing tight torque control in limited space, True Gear’s precision-machined sleeve couplings offer a reliable way to transmit power while minimizing misalignment and backlash, especially in custom or retrofit setups.
Conclusion
Custom torque transmission solutions play an important role in improving efficiency. If you are an OEM engineer looking for custom gears, splined shafts, and couplings, look no further than True Gear & Spline Ltd. We use CNC machining to ensure precise tolerance and top-notch quality. Call 519-653-1301 to get a free quote or learn about all we can do for you.